The Latest from Corn and Soybean Digest
thumbnail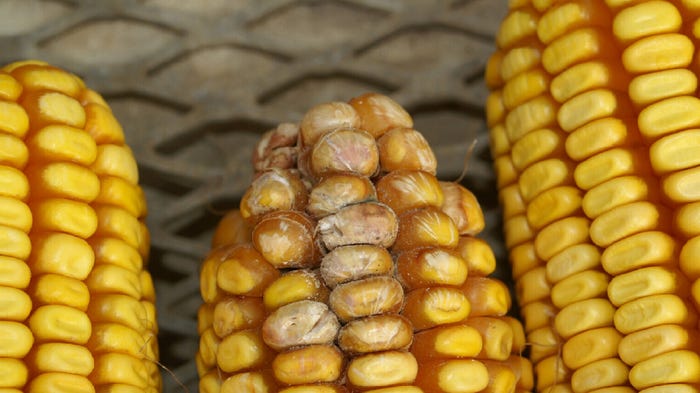
Corn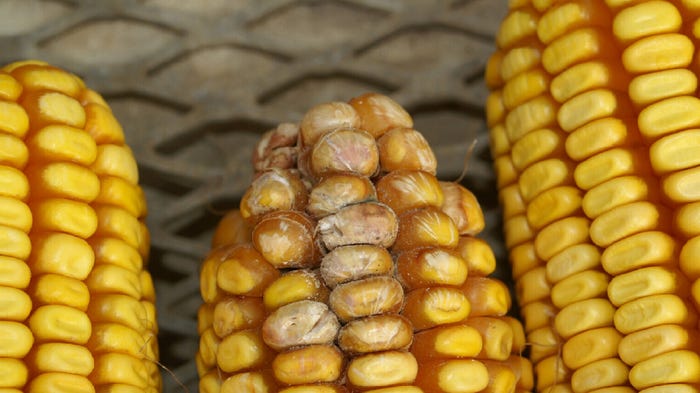
Focus on crop health when fighting fusariumFocus on crop health when fighting fusarium
Constant wet, cold weather early in the season makes corn more vulnerable to fusarium infection.
Market Overview
Contract | Last | Change | High | Low | Open | Last Trade |
---|---|---|---|---|---|---|
Jul 24 Corn | 450 | -2 | 454 | 449.25 | 451.75 | 06:19 PM |
Jul 24 Oats | 358.75 | +7.75 | 360 | 352.25 | 352.25 | 06:17 PM |
May 24 Class III Milk | 18.03 | -0.15 | 18.4 | 17.72 | 18.28 | 06:52 PM |
Jul 24 Soybean | 1177.25 | -2.5 | 1181 | 1172.5 | 1179 | 06:19 PM |
Aug 24 Feeder Cattle | 260.55 | +2.25 | 261.55 | 258.35 | 258.9 | 06:04 PM |
May 24 Ethanol Futures | 2.161 | unch — | 2.161 | 2.161 | 0 | 10:51 PM |

Copyright © 2019. All market data is provided by Barchart Solutions.
Futures: at least 10 minute delayed. Information is provided ‘as is’ and solely for informational purposes, not for trading purposes or advice.
To see all exchange delays and terms of use, please see disclaimer.
All Corn and Soybean Digest
Subscribe to receive top agriculture news
Be informed daily with these free e-newsletters