The Latest from Corn and Soybean Digest
thumbnail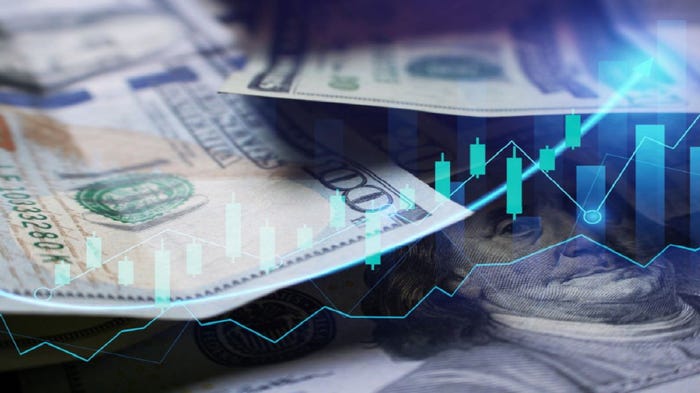
Farm Business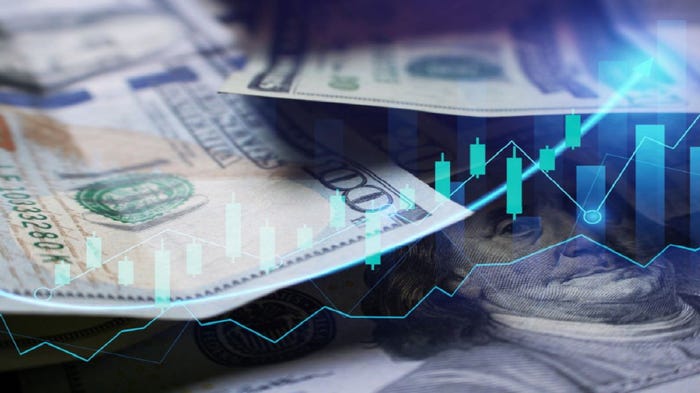
On the horizon: Late payments and carryover debt for farmsOn the horizon: Late payments and carryover debt for farms
Before asking to restructure your debt, do a self analysis to see what caused the issue.
Market Overview
Contract | Last | Change | High | Low | Open | Last Trade |
---|---|---|---|---|---|---|
Jul 24 Corn | 452 | unch — | 452.5 | 451.5 | 451.75 | 12:09 AM |
Jul 24 Oats | 351 | -2.75 | 354.25 | 342.5 | 354 | 11:29 PM |
May 24 Class III Milk | 18.28 | +0.1 | 18.28 | 18.28 | 18.28 | 10:00 PM |
Jul 24 Soybean | 1180.5 | +0.75 | 1180.75 | 1178 | 1179 | 12:09 AM |
Aug 24 Feeder Cattle | 258.3 | +2 | 258.8 | 254.25 | 256.425 | 06:04 PM |
May 24 Ethanol Futures | 2.161 | unch — | 2.161 | 2.161 | 0 | 09:38 PM |

Copyright © 2019. All market data is provided by Barchart Solutions.
Futures: at least 10 minute delayed. Information is provided ‘as is’ and solely for informational purposes, not for trading purposes or advice.
To see all exchange delays and terms of use, please see disclaimer.
All Corn and Soybean Digest
Subscribe to receive top agriculture news
Be informed daily with these free e-newsletters